Invited Speaker
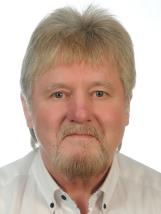
Prof. Wolfgang Osten
Institute of Applied Optics, University Stuttgart, GermanySpeech Title: Erosion Monitoring in harsh environment and monitoring of spray-coating processes by digital holography
Abstract: A feasibility study for erosion measurements under extreme environmental conditions inside the ITER Tokamak is described. The ITER project is the next step in the transition from experimental studies of plasma physics to full-scale electricity-producing fusion power stations. It fuses the hydrogen isotopes deuterium and tritium into helium thereby releasing a high energy neutron. In order to start the fusion reaction the temperature has to be about 150 million Kelvin, creating a plasma. Because there is no material that could withstand such high temperatures, the plasma is guided, contactless, by magnetic fields within the vacuum chamber. However, these fields are not fully closed, resulting in partial plasma contact particularly in the divertor region. This leads to wear effects, affecting the overall performance and reliability of the Tokamak and potentially generating metallic dust. Thus, there is a need for the regular measuring of the erosion and deposition at the wall once the Tokamak starts operating. An erosion and deposition monitor able to measure the changes in the surface shape with a depth resolution of 10 μm is planned. The measurement will be done not on the whole internal surface of the Tokamak but on two surfaces of the divertors that endure high rates of erosion and deposition, each of a size of 10x30 cm². Due to the high temperature and radiation it will not be possible to have the measuring system inside the Tokamak, for this reason the measurements will be performed remotely. Hence the opto-electronic instruments (detector, laser, controlling electronics) will be located at a distance of about 40 m from the surface to be measured. It will be shown that long distance shape measurements in challenging environmental conditions (vibrations and long distance) can be done by two wavelength digital holography and thus this technique could be used for the future erosion monitoring inside the Tokamak.
In addition a method for residual stress analysis of ceramic coatings by applying a laser for quasi nondestructive material removal and measuring the 3D displacement around the machined area by means of high-resolution digital holography is described. The residual stresses are retrieved by numerical calculations using the finite element method (FEM) from the measured 3D displacements, the profile of the machined hole and the material parameters of the coating and substrate. Experimental results on thermal spray coatings together with discussion of the difficulties, work in progress, potential of the method, and comparative measurements by the hole-drilling method are presented.